Condition Monitoring
Why Condition monitoring?
On-line monitoring system installed in power production plants ensures continuous monitoring of exploitation and is a critical step toward predicting mechanical behavior.
The real benefit is the predictive capability for malfunctions and identification of irregularities in system behavior, which can significantly improve repair planning and scheduling and can also prevent additional damage from occurring.
Modern monitoring systems include vibration monitoring, monitoring of electrical parameters and process parameters (temperatures, pressures, flow etc.). System must include continuous measurement, trending and database creation of all measured data. Substantial and well-structured database ensures organized and cost effective maintenance planning.
Repair works based on the exploitation state can significantly reduce the maintenance cost, up to 50 %. Modern monitoring systems are based on network communication and data transfer with other systems installed in power plants using standard industrial protocols (Modbus, Profibus).
Benefits of condition monitoring
Efficient repairs
Better maintenance planning
Permanent change detection
Damage prediction
Damage prevention
Fault diagnosis and detection
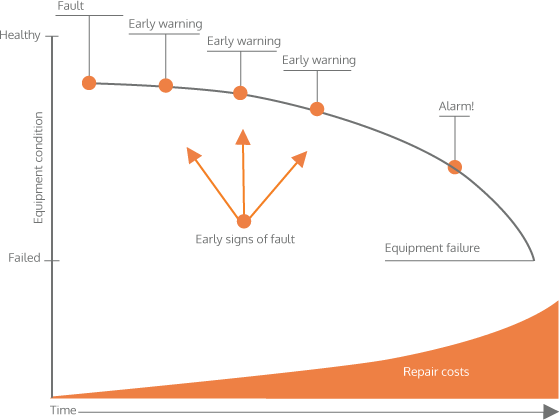
Fault analysis process - Hydro
Knowledge and experience in the field of dynamics, vibrations and strain measurements are based on a number of years of practice in providing solutions to our clients. When it comes to quality assurance, measurements are a key component for predictive maintenance and diagnostic fault testing.
However, the importance of measurements is secondary to the need to isolate the problem and offer effective solutions.
Our knowledge is implemented in our Machine Condition Monitoring software CoDiS, helping our customers identify and anticipate faults and make more efficient maintenance plans.
" Real benefits of condition monitoring are fault prediction and prevention. "
CoDiS Machine Condition Monitoring system
The CoDiS system is a continuous online condition based monitoring system for hydro and turbo generators and electric motors. CoDiS Monitoring and diagnostic capabilities enable the integration of different monitoring technologies (e.g. vibrations, air gap, magnetic field, hydraulic quantities, electric quantities and process quantities) into a single platform and one database. The system is based on open software architecture which enables flexible configuration of the system to facilitate customization and future upgrades.

CoDiS architecture
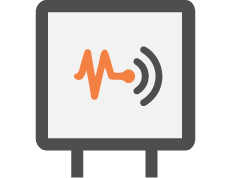
Front-End Components
Installed sensors
and terminal boxes
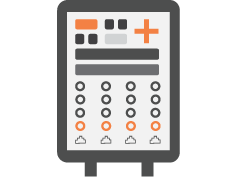
Protection controller
Instrument
+ industrial cabinet
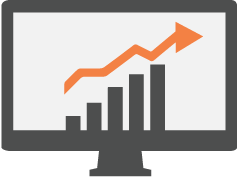
Diagnostic software
Server PC
+ CoDiS application
System layout
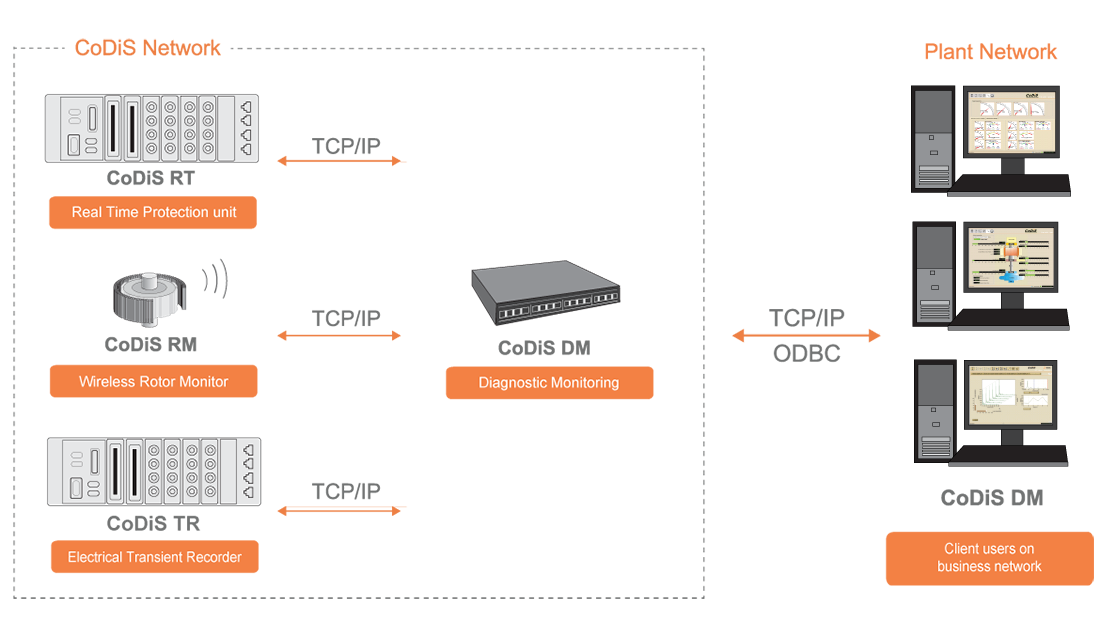